Keynote Presentation
ESG/Sustainability: A Smart Decision That Goes Beyond Regulatory Compliance
Barton White, Kymera International

Barton White is the CEO of Kymera International, a global leading specialty materials and services company with manufacturing sites in 9 countries. Barton was born and raised in Montreal, Canada and currently lives in Raleigh, NC. He began his professional career as a Research Chemist for ICI Chemicals and later held various commercial and management positions in the copper and aluminum powder sectors in Canada, the U.S. and France. Born in Canada, Barton attended Concordia University in Montreal where he received a Bachelor of Science degree in Chemistry and an MBA.
Powder Injection Molding Tutorial
Matthew Bulger, ATPM Consulting
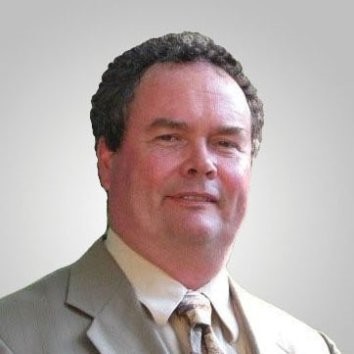
Matt has been involved in the area of metal injection molding (MIM) for more than 30 years. Matt received his MS in Materials Science from Rensselaer Polytechnic Institute and a BS in Physics from Carnegie – Mellon. In 2017, Matt received MPIF’s Distinguished Service to Powder Metallurgy Award which recognized his long-term contributions and achievements to the PM industry. Matt has been very involved with MPIF throughout his career, holing the offices of MPIF President and MIMA President (Metal Injection Molding Association) President, and MIMA Standards Chairman.
Currently Matt is with atpmconsulting. Prior to forming his consultant business, Matt held positions with NetShape Technologies – MIM, as the MIM General Manager, FloMet as the Quality & Materials Engineering Manager, and Remington Arms as a Process Engineer. In addition to instructing the Powder Injection Molding Tutorial at the International Conferences on Injection Molding of Metals, Ceramics and Carbides, Matt is has instructed at MPIF’s PM Sintering Seminars.
Comparison of MIM & Conventional PM Material Properties, Cost Considerations & Other Business Case Factors for Aftermarket Medical Hardware Component
Comparison of Four Different Manufacturing Processes (Production Intent MIM, Machined from Millet, Metal AM and MIM Rapid Prototyping) For Pre-Production Prototypes
Jason Osborne, Alpha Precision Group
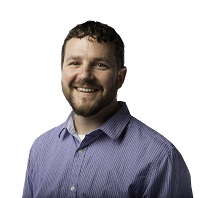
Jason’s 20+ years in the MIM industry has included roles in manufacturing, process control, product development and engineering management. In 2015, Jason founded Neota Product Solutions, initially focused on bringing product development and prototyping resources to the MIM community and later grew into a standalone manufacturing operation. In June of 2023, Neota was acquired by APG-MIM and Jason assumed his current role as VP of Advanced Engineering. Jason is a six sigma blackbelt and received his B.S. in Plastics Engineering from Penn State Behrend.
Metal Injection Molding of Corrosion Resistant Alloys
John Johnson, FAPMI, Novamet/Ultra Fine Specialty Products
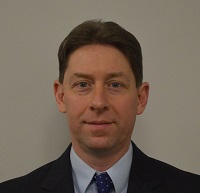
Dr. Johnson joined Novamet in 2020 as Vice President of Operations and Technology for both Novamet and Ultra Fine Specialty Products. Prior to joining Novamet, he was Vice President of Technology at Elmet Technologies. He previously held various R&D positions at ATI Firth Sterling, Kennametal, Singapore Technologies, Alcoa, Howmet, and Penn State. He has a B.S. from Virginia Tech, a M.S. from Rensselaer Polytechnic Institute, and a Ph.D. from Penn State. He is the Roadmap Chairman for the MPIF Technical Board and was awarded APMI Fellow status in 2019.
Capitalizing on Hybrid Metal 3D Printing to Reduce Tooling Leadtime
Thomas Houle, Matsuura Machinery USA
Several MIM-Like Sinter-Based AM Processes
Animesh Bose, FAPMI, Desktop Metal
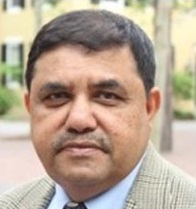
Dr. Animesh Bose has been involved in the area of powder metallurgy (PM) for more than 40 years.
He has published over 125 papers, 10 patents, and 4 books. He currently serves as the VP of Special Projects, Desktop Metal, a company involved in 3D printing. He is a fellow of ASM International and APMI International. He was the Divisional Editor for the section on Metal Injection Molding for ASM Handbook, Volume 7 (Powder Metallurgy), 2015. He has served as the co-chair for the MPIF MIM Conference, Powdermet, and is the founding co-organizer of Tungsten, Refractory, and Hardmaterials Conference Series. He is the Tech Board representative for the Association of Metal Additive Manufacturing (AMAM) and is the Chair for the AMAM Standards Committee. He will be serving as the Co-chair for the AMPM2022 at Portland, OR.
Utilizing Metal Injection Molding (MIM) in the Manufacture of a Large Tungsten Heavy Alloy WHA - Firearms Component—Problems and Solutions
Gaetano Mariella, Polymer Technologies Inc.
Gaetano (Guy) Mariella is a veteran of material science and metallurgy with over three decades of engineering experience designing solutions for the military, aerospace, medical, and electronics industries.
Currently the Chief Technology Officer and Director of Engineering at PTI in Clifton, New Jersey, which offers precision integrated injection molding services, Guy leads the engineering team in developing and delivering best-in-class products that leverage the advantages of combining both engineering polymers and metals.
His innovative thinking and development of refractory powder metal techniques and parts have helped hundreds of clients—from Boeing, to the US Military, to major healthcare providers—solve complex problems and have led to the creation of groundbreaking medical devices and mission-critical military hardware.
Prior to PTI, Guy’s work in powdered metallurgy engineering includes over 20 years of experience at Bayer Material Science and HC Starck Inc. (formerly Kulite Tungsten Corporation) where he served as Director of Process Control and Development. In this role, he was responsible for production and process control, new process creation, and research and development. He spent another 10 years at Kulite Semiconductor Products Inc. where he served in multiple roles including Director Supply Chain, Senior Manufacturing engineer and Program Manager.
A leader in the field, he has presented several papers at major conferences and holds multiple patents He estimates that throughout his career he has sintered over 30 million lbs. of powder metal products.
He received his degree in Metallurgy and Material Science from NYU Tandon / Brooklyn Polytechnic.
Development of Water-Atomized Powder for Binder Jet 3D Printers
Keisuke Itotsubo, Epson Atmix
MIM S7 Tool Steel Properties Versus Composition and Processing
Dwight Webster, Advanced Metalworking Practices
Machine Setup and Significant Parameters to Adjust the MIM Molding Process
Marko Maetzig, ARBURG GmbH + Co KG
A Review of the Attributes and Debinding Methodologies of Binders Utilized in Metal Injection Molding Process
Lane Donoho, Advanced Metalworking Practices
Carbon Foot Print for MIM Furnaces
Maximilian Mungenast, Carbolite Gero GmbH & Co. KG
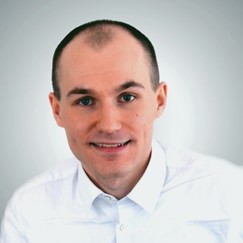
Max received BS in Mechanical Engineering / Product Development at the University of Pforzheim. Upon completion of his studies, Max continued as an academic employee at Pforzheim University’s Institute for Precious and Technology Metals,. His work expereinces and activities include materials science, magnetic recycling, co-development of a metal 3D printing process. In 2022, Max joined Carbolite Gero GmbH & Co. KG and is currently workign in an international sales and product developmentsales role as the export area sales manager.
Metal Additive Manufacturing Complements, ot Competes, with Metal Injection Molding
Tibor Gyorfi, Metals, Endeavor 3D
Feedstock Development for Metallic Material Extrusion (MEX) of Aluminum Alloys
Margarete Hufnagl, Montanuniversitaet Leoben
Dry Ice - A Sustainable Mold Cleaning Solution
Steve Wilson, Coldjet
Steve Wilson is the Director Dry Ice Cleaning Applications & ESG at Cold Jet LLC, responsible for guiding dry ice cleaning solutions for all industries worldwide. He has over 35 years of experience in the plastics, rubber & composites industries before joining Cold Jet 12 years ago. Steve has written numerous white papers on dry ice solutions for various applications. He serves as President for the Ohio Valley Section of the Society of Plastics Engineers and is the current DPM for AMPP SP21514 Dry Ice blasting on Metallic & Nonmetallic Substrates.
Case Study: Utilizing Additive Manufacturing for Rapid Production of MIM Tooling
Tim Will, Ruger Precision Metals
Combining Quantitative Fractography Tools and Statistics-Based Models to Estimate Fatigue Life in Porous Metals
Ian Wietecha-Reiman, Penn State University
Comparison of Four Different Manufacturing Processes (Production Intent MIM, Machined from Millet, Metal AM and MIM Rapid Prototyping) For Pre-Production Prototypes
Jeff Howie, Nichols Portland Inc.
Additive Screen Printing: Industrialized AM Technology for Powdered Metals, Ceramics, and Beyond
Eric Bert, Exentis North America
Eric Bert holds a BSME from UMass-Amherst and has a 30+ year track record in disruptive manufacturing technology introduction and management. Eric currently serves as President of Exentis North America and is responsible for building a North American beachhead for Switzerland based Exentis Group AG. Prior roles in Additive Manufacturing included; SVP Commercial at Inkbit, COO at 3DMEDiTech, SVP Global Sales at ARCAM (a GE Additive company), and SVP at Stratasys North America during its high growth period. Earlier, Eric held technology and management positions in the high-volume printed circuit and electronics assembly sector. He further worked as an expat in Thailand and Australia building and running manufacturing operations.
Hydrogen Delivery Issues Requires Sintering Atmosphere Options
David E. Wolff, NEL Hydrogen
Dave Wolff has over 40 years of project engineering, industrial gas generation and application engineering, marketing and sales experience. He has been a Sales and Marketing leader for hydrogen generation technologies since 1999. Dave holds a degree in Engineering Science from Dartmouth College. He has an extensive background in hydrogen generation at large and small scale, hydrogen distribution, storage and industrial utilization, as well as application knowledge across a diverse range of industries.
Processing of Mesostructured Stainless Steels Using FFF Technology
Juan Jiménez Alumbreros, Universidad de Castilla-La Mancha (UCLM)
Lithography-Based Metal Manufacturing as a Complementary Process to MIM
György Attila Harakály, Incus GmbH
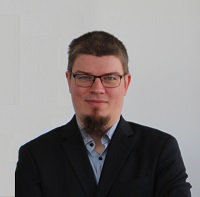
Dr. György Harakály is the Head of R&D Materials at Incus GmbH, an Austrian system provider for an innovative lithography-based Metal Manufacturing (LMM). He obtained his B.S and M.S. degrees in the Budapest University of Technology and Economics in the fields of chemical engineering and pharmaceutical engineering. Afterwards, he received his Ph.D degree from Technische Universität Wien, Austria, where his research was focused on the development of photopolymerizable resins for the AM of dental applications. Since 2021 he is responsible for the research and development at Incus, bringing his expertise in polymer chemistry, material science and additive manufacturing.
Metal Manufacturing in Space with Sintering Based Extrusion 3D Printing
Fatou Ndiaye, University of Louisville
Physical Characterization Methods for Metal Powders
Jack G. Saad, Micromeritics Instrument Corporation
Towards Binder Jetting of Graphene-Reinforced Copper for Improving Mechanical and Electrical Properties
Kaustubh Deshmukh, Virginia Tech, Department of Mechanical Engineering
Process Optimization Using Simulation Software
Jacob Michaelson, SIGMASOFT Virtual Molding
Thermal Conductivity Characterization Using the Hot Disk Method
Artem Trofimov, Orton Ceramic Foundation
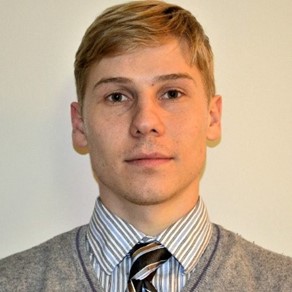
Artem is from Odintsovo, Moscow region, Russia. He graduated from Russian State University of Aviation Technology in 2012 with B.S./M.S. in physics. The same year he joined Clemson University where he received his M.S. degree in 2014 and Ph.D. in 2018 both in materials science and engineering. His Ph.D. research was focused on ceramic scintillators. Following completion of his Ph.D., Artem joined Oak Ridge National Laboratory in 2018 as a Postdoctoral Fellow working in the area of thermophysics and thermal characterization of materials. After finishing his fellowship at ORNL in summer 2021, Artem secured a position at Orton Ceramic Foundation continuing his work in the field of thermophysics and materials characterization.