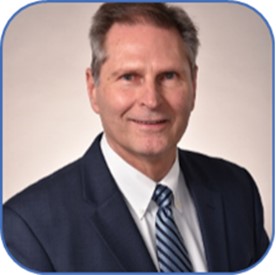
Keynote Presentation
Medical Device Challenges for MIM and PM Components
Gary Jaworek- Senior Principal Engineer Johnson & Johnson, Medical Devices
Gary Jaworek is a Sr. Principal Development Engineer for the Med Tech division of Johnson & Johnson. Gary has been involved in new component development for medical devices for the past 19 years focusing on Metal Injection Molding as well as other metal and polymer manufacturing processes. Gary has had the opportunity to work with suppliers from all around world to meet the design requirements for J&J medical devices while striving to advance the technology for powdered metal components. Gary and his team were involved in two components awarded an MPIF design excellence awards for Medical Devices in 2011 and 2015. Gary is a certified J&J Blackbelt, PMP, with degrees in Mechanical Engineering, as well as a Master of Business Administration.
Gary will share examples of current Johnson & Johnson products while providing information related to design challenges that are occasionally encountered when designing new components for robotic and hand held surgical devices. These challenges include size, geometry, tooling and material processing concerns that need to be overcome. Gary will also discuss how J&J has improved its speed to market and design processes utilizing metal additive manufacturing during its process development. Lastly, Gary will introduce some of J&J Sustainability Goals that they are working on both internally and with their suppliers.
17-4PH Stainless Past and Present
Tim McCabe, OptiMIM
17-4PH has been a key material in Metal Injection Molding. A review of 17-4PH over the past 30 years will be presented and compared with wrought material.
Metal Injection Molding of F75 (Co-28Cr-6Mo)
John L. Johnson, FAPMI, Novamet/Ultra Fine Specialty Products
Due to a combination of strength, wear resistance, corrosion resistance, and low magnetic permeability, Co-28Cr-6Mo is used in diverse applications ranging from smart phones to surgical implants. Historically cast to ASTM F75 specifications, many Co-28Cr-6Mo components are suitable for metal injection molding. Achieving F75 properties in the as-sintered state requires control of the interstitial content and microstructure, which are dependent on the starting powder chemistry and the sintering atmosphere as shown from sintering studies of metal injection molded F75 powders produced by gas- and water-atomization. The effects of hot isostatic pressing and heat treatment to further improve the mechanical properties are also investigated.
Production of Permanent Magnets from Recycled Nd-Fe-B Powder Using the Extrusion Debonding Sintering Process
Stefan Rathfelder, Co-Authors - Santiago Cano, Christian Kukla, Carlo Burkhardt, Clemens Holzer
The number of permanent magnets based on rare earths such as neodymium is increasing significantly from year to year. They are used, for example, in drives for electric cars or wind turbines. The SUSMAGPRO project, funded by the European Union, aims to produce permanent magnets from recycled neodymium-iron-boron (NdFeB) material using the extrusion debonding sintering (EDS) process. Powder for the process is produced using the highly efficient HPMS process from End-of-Life magnets and blended with polymeric material and additives to form a granulated feedstock. Instead of injecting the powder melt into a closed mold as in powder injection molding, the material continuously pressed through an extrusion die. This produces a strand of any length that has the cross-section of the extrusion tool's mold. Cut into sections, the green parts are then debinded and sintered under inert gas atmosphere. The talk discusses the production steps from powder production to the final part.
Plasma Powder Production for MIM Applications
Jérôme Pollak, Tekna
The Metal Injection Molding process starts with the selection or creation of the right feedstock. RF plasma technology can provide high-quality metallic powders with controlled grain size, low interstitial content, high density as well as high level of purity which helps to produce a homogeneous feedstock that is favorable for metal injection molding process. Spherical Ti64 titanium, Nickel, Tungsten and Tantalum powders manufactured by RF plasma technology are well suited to meet the Metal Injection Molding needs. The presentation will describe RF plasma technology production method for micro-sized metallic powder devoted to MIM applications.
Role of Nitrogen and Other Minor Alloying Elements on Microstructural Evolution During the Heat Treatment of 17-4 PH Grade Stainless Steel
Derek J Shaffer, Pennsylvania State University, Co-author – Todd Palmer
Small variations in alloying elements that are often overlook in 17-4 PH stainless steel can significantly impact the heat treatment behavior of the alloy. Specifically, interstitial elements like nitrogen and oxygen have been observed to differ almost ten times in weight fraction in powder metallurgy and additively manufactured components compared to conventional wrought material. Significant changes to phase stability of both major phases, such as austenite, and minor phases, such as carbonitrides, due to such compositional changes necessitate a new, more detailed understanding of the evolution of phases in 17-4 PH stainless steel components made using powder metallurgy and additive manufacturing techniques. In this work, both aging and solution heat treatments are evaluated with respect to compositional impacts on developed microstructures. The impact of these differences in microstructure is then also shown through the differences in microhardness and tensile properties.
Comparison of Binder-Jet and MIM
Animesh Bose, FAPMI, Desktop Metal, Inc.
Binder-jet is currently established as the additive manufacturing (AM) process suitable for the mass production of complex shaped metal components without the use of any tooling. The process has a number of similarities to the relatively mature process of Metal Injection Molding (MIM) along with some major differences. This presentation will compare and contrast the two processes and also discuss the advantages and limitations.
Material and Process Details Needed to Successfully Develop Debinding and Sintering Recipes for Binder Laden Metal Powder Components (MIM or AM)
Stefan Joens, Elnik Systems, LLC
A Review of Vacuum Induction Melting Inert Gas Atomization (VIGA) Technology as Well as Modified Efficient Water Atomized Technology
Jerome Stanley, North American Höganäs Co.
Fine powder production capability can be extended with state of the art Vacuum Induction Melting Inert Gas Atomization (VIGA) technology and highly efficient modified water atomizing technology. Metal powders derived from these novel technologies are suitable for MIM processes as well as for additive manufacturing based on binder jetting or selective laser melting. The wide powder range covers all type of applications requirements ranging from Aerospace to General industry.
Additive Manufacturing of Aluminum Alloy by Metal Fused Filament Fabrication (MF3)
Luke Joseph Malone, Co-author – Sundar Atre
This research studies metal-fused filament fabrication (MF3) for manufacturing aluminum alloy parts. An aluminum alloy powder-based feedstock with a polymer-binder system will be extruded via capillary rheometry to form a filament. The filament will be used to print green parts that are involved in a two-step debinding process combining solvent and thermal extraction of the polymer binder, then sintered in a partial vacuum. Resulting grain structure, sintered density, and mechanical properties will be characterized and compared to metal injection molded (MIM) specimens. The main objective is to gain an understanding of the MF3 process characteristics and the ensuing material properties and microstructure through carefully designed experiments and computer simulations, therefore creating additive manufactured components from a common lightweight metal. The overarching goal is to enable rapid, predictable, reproducible, low cost, and accurate production of metal parts with 3D features, thereby significantly expanding the current additive manufacturing capability.
Adapting Metal Injection Molding (MIM) Feedstocks For 3D Printing Non-Ferrous Alloy Structures via Metal Fused Filament Fabrication (MF3)
Kameswara Pavan Kumar Ajjarapu, University of Louisville
Metal fused filament fabrication (MF3) 3D printing process is used to fabricate 3D metal components by combining fused filament fabrication and sintering process. To adapt metal injection molding (MIM) feedstocks to 3D printing via MF3, it is important to understand how materials will behave in the MF3 3D printing process due to changes in powder-polymer composition and thereby affect green part quality, precision and processability. In this work, unfilled filaments and highly filled copper alloy filaments were printed via FFF at different extrusion temperatures and print speeds. Viscosity and shear rate were correlated to their corresponding print temperature and print speed to generate process maps for each material, by locating the viscosity and shear rate combination beyond which the material fails to print. Further, rheological, thermal, and mechanical characterization was performed to identify how material properties of the filament affect printability.
Exploring Automated Bending Process for MIM Part Dimensional Correction
Douglas Kaercher, The Arc Group Worldwide
When MIM parts have dimensional non-conformance due to distortion, they must be corrected to meet the customer requirements. This can be done a variety of ways from manual tweaking with hand tools up to high force compressing and bending with hydraulic press tooling. When the part variation is relatively small, the parts can be processed effectively into conformance with a fixed process that reshapes the parts to the same dimensions. However, when dimensional variability is large the parts need to be processed to with a method that is adjustable to account for the degree of distortion. This is due largely to the presence of spring back that is exhibited in most of the MIM steels. Various methods to achieve variable correction results have been utilized but many of them are labor intensive and dependent on high operator skill level. I would like to explore the effectiveness of utilizing a servo-driven bending mechanism with measured feedback of the initial size of the part to automatically bend the part into the correct dimension. The process will tune the bending parameters based on the degree of the distortion of each part to create a variable and automatic correction process.
Costing of MIM Components
Matt Bulger, ATPM Consulting
A review of Metal Injection Molding costing techniques, common estimation mistakes and oversights when costing MIM components.
Solvent Debinding: A Comparison of the Overall Efficiency of Traditional Debinding Solvents to Halogenated Azeotropic Solvent Mixtures.
David Ferguson, MicroCare, LLC
We will start with a brief review of the different methods and common fluids used for debinding. Then share an update to our laboratory work regarding solvent debinding of MIMs parts. Data will be shared on a range of samples whose weights were recorded at the green and brown stage and plotted to identify ideal debinding times. We will finish up by providing a short summary update on the current regulatory reports that have been in the news regarding some of the historical debinding fluids, and how these regulations may affect fluid availability.
Impact of Gas Guiding in an Improved Debinding and Sintering Furnace for AM Parts: CFD Simulations and Initial Experimental Results
Tim Ohnweile, Carbolite Gero
Nowadays precision components fabricated by various methods of the AM process have to fulfill high requirements to their geometry and suffer from a high pricing pressure. During production differences occur in carbon content and distortion in dependence of the position of the part inside the sintering furnace, because the binder is carried away inhomogeneously in the usable volume or the uniformity is not good enough. Hence, high costs are generated, and time is lost due to empirical loops to improve the process.
In order to overcome these problems, simulations are carried out to improve the situation beforehand. By a Computational Fluid Dynamics (CFD) approach, the geometry of the furnace, the gas inlet and outlet geometry as well as the geometry of the whole sample load and the shape of each individual part is taken into account: The aim is to improve the furnace in a first step in such a way to get a uniform gas distribution inside the usable volume, which is as much as possible independent of the specific furnace load. As the furnace load for sure influences the gas paths, the second step is to find the optimum load and sample orientation with as much samples inside the furnace as possible together with the right settings of gas flow.
Initial simulation results will be presented, which were leading to a new generation of debinding and sintering furnaces beginning from small up to industrial sized models as required i.e. for MIM.
Application of Hot Disk Transient Plane Source for Thermal Conductivity Evaluation During Metal Injection Molding: Case of Metal Powders
Artem A. Trofimov, Orton Ceramic Foundation
Thermal conductivity can be used for a variety of purposes in powder injection molding (PIM) of both metal (MIM) and ceramic (CIM) materials and additive manufacturing (AM): simulations/modeling, optimization of the processing/manufacturing parameters, quality evaluation of components, estimation of the porosity, etc. Meanwhile, only a limited number of techniques are available for the assessment of thermal conductivity of the initial powders or a feedstock (powder + binder), and an even smaller number of instruments are suitable for thermal conductivity measurements at every stage of the MIM process. In this work, Hot Disk Transient Plane Source technique is proposed for the evaluation of the thermal conductivity of the intermediate as well as the final parts obtained throughout MIM. Potential application of the Hot Disk technique to the characterization of the solid samples (such as “green”, “brown”, sintered parts) will be discussed, and the focus of this presentation will be given to the evaluation of the metal powders.
Dry Ice Cleaning in MIM - Who Needs It?
Steve Wilson, Cold Jet LLC
There’s no doubt that molds are a mission critical asset and require timely, proper & efficient maintenance to ensure uptime and part quality. And, if there’s any segment of injection molding that has to clean molds frequently, its MIM processors. No matter how large or small of a molding operation, custom or captive, MIM processors deal with frequent mold fouling from the binders used in MIM. Keeping Mold cavities clean and vents open is critical for successful molding. How you clean your molds can mean the difference between mediocre performance and good OEE scores translating to high-profit productivity. Traditional methods not only can create extended downtown, but can cause mold wear to parting lines, sealing surfaces and various surface finishes. This presentation discusses the top 5 reasons MIM molders are turning to dry ice solutions to clean their molds while they are still in the machine, at operating temperatures, in a very quick and effective manner, without causing and wear to the tool.
This presentation will also provide the attendee a working knowledge of the science and process of how dry ice cleaning works and how to adapt it to various other cleaning opportunities in their factories, i.e. screw cleaning, deflashing, surface preparation, etc. This presentation includes supporting research from several independent studies, along with several industry case studies, pictures and videos.
Powder Production and Metal Injection Molding (MIM) of a Novel Light-Weight, High-Strength, Non-Magnetic Steel, Compared with Ti6Al4V Alloy Alternative
Paul A. Davies, Sandvik Osprey Ltd., Co-authors: Rudolf Seiler, Thorsten Staudt, Eleonora Bettini, Luke Harris
Reducing the weight of Metal Injection Molding (MIM) components, manufactured for modern information & communication technology (ICT) applications, is attractive, as the weight of hand held devices have increased in recent years. Components like smart-phone camera lens brackets, have increased in size with the addition of more lenses, range finders and flash lights. These components have high aspect ratios, requiring high specific yield-strength, stiffness, high sintered density and hardness, with the addition of demanding aesthetic requirements, requiring high levels of polish performance. This was achieved with the development of a lightweight, non-magnetic steel powder, produced by inert gas atomization, that incorporate high proportions of aluminum and titanium, which aid grain refinement and precipitation strengthening. While aluminum & titanium are low density elements, they also generate high levels of heat of combustion and present an increase explosion hazard in fine powder form. However, optimized alloy designs balance the safety risks of the manufacture of metal powders with material performance and density. The sintered density, mechanical performance, corrosion resistance and magnetic response are compared with Ti6Al4V alloy, as an emerging viable alternative MIM material.
Development of Biobased Feedstock for PIM-Like Extrusion-Based Additive Manufacturing
Nicolas Charpentier, Femto-ST, Université de Franche-Comté, Co-authors – Thierry Barriere, Frederic Bernard, Nathalie Boudeau, Alexandre Gilbin
Extrusion-based Additive Manufacturing of PIM feedstock is a field of 3D printing in full extension, but the binder used is often a derivative that is optimized for PIM and not Additive Manufacturing. This work seeks to develop a new binder for this process with an ecologic prerequisite of being composed of biobased polymer and additives. The development of a PLA binder for PIM-like Extrusion-based Additive Manufacturing process is described in this work, investigating the influence of its composition on the process from the green part to the finished densified part. The binder was used with different powder to research the influence of the powder granulometry in the feedstock, and of the printing parameters on the process.
Ensuring Hydrogen Availability to Metal Injection Molding Operations During Supply Chain Challenges
David Wolff, NEL Hydrogen
Over the last 10 years, major changes have occurred in the hydrogen supply/demand situation, especially in the US and bordering manufacturing communities in Mexico and Canada. For hydrogen users for manufacturing, hydrogen has become recognized as a raw material requiring concern due to supply chain complexity and delivery/storage challenges.
For hydrogen supply there may be on-site hydrogen generation or, where market conditions permit, hydrogen may be delivered in liquid or compressed gaseous form. Historically, liquid hydrogen has been the preferred approach in locations where it has been generally available and economic, while delivered gaseous hydrogen or on-site hydrogen generation has been the options when liquid hydrogen has been unavailable or expensive. Liquid hydrogen has been widely available and economic in North America for decades, and availability is good in several areas in Europe. Besides those specific geographies, liquid hydrogen has been prohibitively expensive or entirely unavailable. Hence liquid hydrogen delivery has been the preferred supply approach in North America and where available in Europe, and delivered gas or on-site generation have been used everywhere else.
With industry investment in technology development, standardization and mass production, the capital cost of hydrogen generation equipment has decreased markedly over the past 20 years, and the operational efficiency and reliability of the equipment has increased markedly. Mass production makes it possible to recognize issues in an equipment population and make the changes prospectively to ship better equipment. The reliability and economic benefits of on-site hydrogen have now been widely demonstrated for over two decades.
Chemical-Mechanical Surface Finishing of MIM and Binder Jet Components: Observations and Recommendations
Lane Winkelmann, REM Surface Engineering, Co-authors: Justin Michaud, Agustin Diaz, Lane Winkelmann
Chemical-Mechanical Polishing processes (CMP) such as chemically accelerated vibratory finishing (CAVF) have a long history of success in the Metal Injection Molding (MIM) industry. CMP processes have demonstrated the capability of reducing as-sintered surface roughness with reduced shape alteration and edge radiusing as compared to abrasive-only mass finishing technology. The generated, isotropic surfaces have been shown to improve component function performance and to aid the manufacturing process overall. Metal Binder Jetting (MBJ) is a maturing Additive Manufacturing (AM) process with the potential to produce low-cost components in a high-volume manner without significant tooling or setup costs. While MBJ has many similarities to MIM, there are also some important differences in both surface roughness and their response to surface finishing. These differences should be considered when evaluating MIM versus MBJ (or other forming technologies) for applications where generally low surface roughness characteristics may be required. This presentation will primarily review MIM and MBJ surfaces in various states ranging from as-sintered to highly polished and will briefly compare these results to other forming technologies with a goal of providing the audience with useful information as they evaluate part forming technologies for their applications.
Mitigating Post-Sinter Distortion in MIM via Machining in the Green State
Levi M. Rust, ARC Group Worldwide
In the Metal Injection Molding Industry, manufacturing holes and round parts with critical tolerances can be challenging. Through the sintering process many factors will cause holes or cylindrical shapes to distort, necessitating secondary machining to achieve desired tolerances. This study seeks to determine if green machining can be utilized to correct the roundness or diameter of parts prior to sintering. Ideally, processing in this manner will mitigate distortion and result in the part densifying to the desired dimension. This study will evaluate the effect of machining green parts on the post-sinter dimensions.
Building Confidence Through Virtual Metal Injection Molding
Harshal Bhogesra, SIGMA Plastic Services, Inc.
Driven to optimize product designs, tools and processes to ensure maximum profitability and efficiency for your MIM molding operations, metal injection molding manufacturing companies are turning to ‘Autonomous Optimization’ to eliminate the tedious and costly molding trial and errors on the production floor by running some designs from the entire design of experiment space, in generations, and ingeniously learning from the previous design and moving towards the most optimum solution. We will demonstrate these capabilities, using case studies and prove how success is achieved, even with the most challenging MIM products.
MPIF Standard 35 Metal Injection Molding Materials Standards Update
Michael Stucky, Norwood Medical
Reduction in Shrinkage of Binder Jet Printed Large Stainless-Steel Parts Using Novel Metal Powders
Alexander Paterson, ExOne and Adam Bartel, Tundra
Binder Jet Printing is a rapidly growing section of Metal Additive Manufacturing. Because of its high-speeds and material flexibility, binder jetting stands alone among 3D printing methods as a technology that could transform traditional high-volume manufacturing and bring the design, cost and sustainability advantages of 3D printing to the masses. One of the limitations of the binder jet process is the dimensional instability of large parts caused by shrinkage during the sintering process. With today’s metal powder materials, parts can be printed to 55-60% of full density resulting in shrinkages between 16-22%. The design compensations necessary for this high level of shrink practically limits binder jet part sizes to less than 5 inches, and can also limit feature size variations in a part design. A novel approach to metal powders has resulted in green parts that are printed to >70% of full density resulting in shrinkages <10% while still achieving >98% theoretical density post sintering. These powders allow for the creation of larger and more complex parts to be manufactured due to lower, more isotropic shrink characteristics in the sintering process, resulting in higher tolerance values. For examination, parts larger than 6 inches in diameter were manufactured with the novel 316L powder and were compared to standard binder jet 316L powders. The parts were scanned for distortion and measured against the original CAD model. The external shrinkage rates were also measured and compared.
Corrosion Behaviors of Additively Manufactured H13 and Maraging Steel MS1 Tool Steels for Die Casting Mold Applications
Xuehui Yang, Indiana University - Purdue University Indianapolis, Co-authors: Alan Jones, Yeou-li Chu, Jing Zhang
Corrosion is a major issue in the molding industry due to the harsh operating conditions. Recently, additive manufacturing has been used to manufacture mold components. Additionally, heat treatments are used to improve material properties. It is imperative to understand the corrosion mechanisms in steels exposed to harsh conditions. In this work, the corrosion behavior of two types of additively manufactured molding materials (H13 and maraging steel MS1) were studied. The Tafel polarization and electrochemical impedance spectroscopy (EIS) tests were performed in different mediums, DI water, tap water, DI water with inhibitors and sodium chloride solution. The results show that the anti-corrosion properties depend on the processing and environment. In our study the heat-treated material resisted corrosion the best, followed by as cast. The MS1 material performed better than the H13 material, and as expected, the DI water with inhibitor resulted in less corrosion than DI water, followed by tap water and finally the sodium chloride solution. This investigation will allow insight into the corrosion properties of different mold materials and environments and result in improved mold and tool life.
Sintering Behavior of Binder-Jet Printed H-13
James W. Sears, AMAERO
H13 is a chromium, molybdenum, vanadium hot work steel containing up to 0.4% carbon by weight and is strengthened by martensite and carbides. It is also commonly referred to as DIN 1.2344 or X40CrMoV5-1 steel. It has excellent wear resistance, hot hardness and hot toughness thereby warranting its use in both hot work applications such as die casting. This study has been performed to better understand the sintering behavior of H-13 with the intent of its use for Binder-Jet Printing of tooling for applications in the aluminum die casting industry.
Two Component Micro Powder Injection Molding of Bi-Material Stainless Steel 17-PH and Yttria Stabilized Zirconia
Abu Bakar Sulong, Universiti Kebangsaan Malaysia, Co-authors: Ai-Basir, Nashrah Hani Jamadon, Norhamidi Muhamad
The global trend towards micro products and the necessity for incorporating different functional capabilities within a micro-component have played a significant role towards the evolvement of the two-component micro-powder injection molding (2C-μPIM) process. 2C-μPIM technology provides the opportunity to conjugate different materials within one part with complex geometries at mass production. However, dissimilar materials comprised physical and thermal properties causing huge challenges in the 2C-μPIM process. The main objective is to investigate the processability of stainless steel 17-4PH (SS17-4PH) and 3 mol% yttria-stabilized zirconia (3YSZ) powders through four main parameters in the 2C-μPIM process. It focuses on the effect of different physical and thermal properties on the feedstocks, injection molding, debinding, and sintering parameters. In this study, critical powder volume concentration (CPVC) analysis was carried out to determine the optimal powder loadings required to prepare the SS17-4PH and 3YSZ feedstocks. Typically, the feedstocks were obtained by mixing SS17-4PH and 3YSZ powders individually with a binder system comprised of 60 wt.% of palm stearin (PS) and 40 wt.% low-density polyethylene (LDPE). Afterwards, investigations were carried out to evaluate the rheological properties of the prepared feedstocks at temperatures of 140, 160, and 180 °C. The sequential procedures were employed to process the SS17-4PH and 3YSZ feedstocks by using a plunger type injection molding machine to form micro-sized SS17-4PH/3YSZ green parts. Subsequently, solvent debinding process on the green bi-material micro-parts was carried out in acetone at 70 °C for 40 min. Eventually, thermogravimetric analysis-based thermal debinding process was carried out, and the sintering of the SS 17-4PH/3YSZ micro-sized brown parts were performed in the argon environment at 1250, 1300, and 1350 °C at a heating rate of 10 °C/min for sintering time of 1, 2 and 3 hours. In this research work, the obtained CPVC of SS 17-4PH and 3YSZ powders were 71.7 and 47.1 vol.%, respectively. Based on CPVC analysis, four feedstocks with optimal powder loadings of 69 and 70 vol.% for SS17-4PH and 44 and 45 vol.% for 3YSZ were prepared. During the injection molding process, SS17-4PH and 3YSZ feedstocks with powder loadings of 69 and 44 vol.%, respectively, were utilized to fabricate the green SS17-4PH/3YSZ micro-parts. Around 73.3% palm stearin was removed from the bi-material during the solvent debinding process. The open channels that developed in the solvent debound components helped to eliminate 96 to 99% of the binder in the thermal debinding stage. The density of the bi-material micro-parts after sintering reached 99% of the theoretical density. The sintered parts exhibited linear shrinkage between 9.3 until 17.4% in comparison to green parts. The microstructures from FESEM revealed the bonding between SS17-4PH and 3YSZ. At the interface, the existence of Fe, Ni, Cr, and Zr were ascertained by EDX. EDX layered spectrum analysis that entrained bonding to the generation of the oxide layer and other metallic phases in the process of co-sintering. The areas near to the interface exhibited higher hardness values compared to areas away from it. The tensile strength of the bi-material sintered parts increased with the increase of the sintering temperature. In conclusion, the findings exhibited that SS17-4PH/3YSZ is successfully fabricate through 2C-μPIM process by overcoming the incompatibility in the physical and thermal properties of SS 17-4PH and 3YSZ materials.